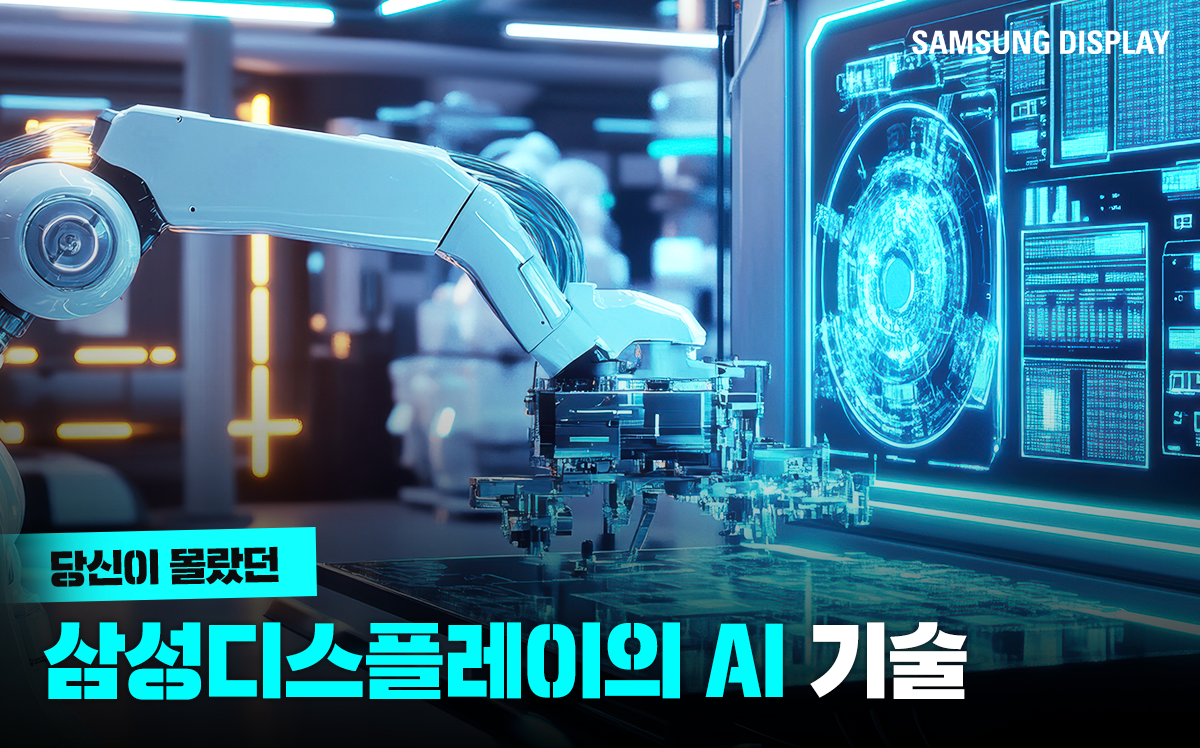
요즘 한창 유행하고 있죠? ‘GPT-4o’ 이미지 생성 기능으로 내 사진을 지브리나 디즈니 같은 유명 애니메이션 스타일로 바꾸는 것. 한국뿐만 아니라 전 세계적으로 선풍적인 인기를 끈 탓에 샘 울트먼 오픈AI CEO가 “GPU가 녹아내리고 있다”라고 말하기도 했는데요. 일반인들에게도 한층 더 친숙해진 AI 기술은 인공지능 전환(AX)을 통해 기업과 산업에도 새로운 혁신을 가져오고 있습니다.
*인공지능 전환(AX, AI Transformation): 기업이 인공지능을 활용해 산업의 체질을 바꾸고, 단순한 작업을 자동화해 궁극적으로 산업 생산성을 극대화하는 것.
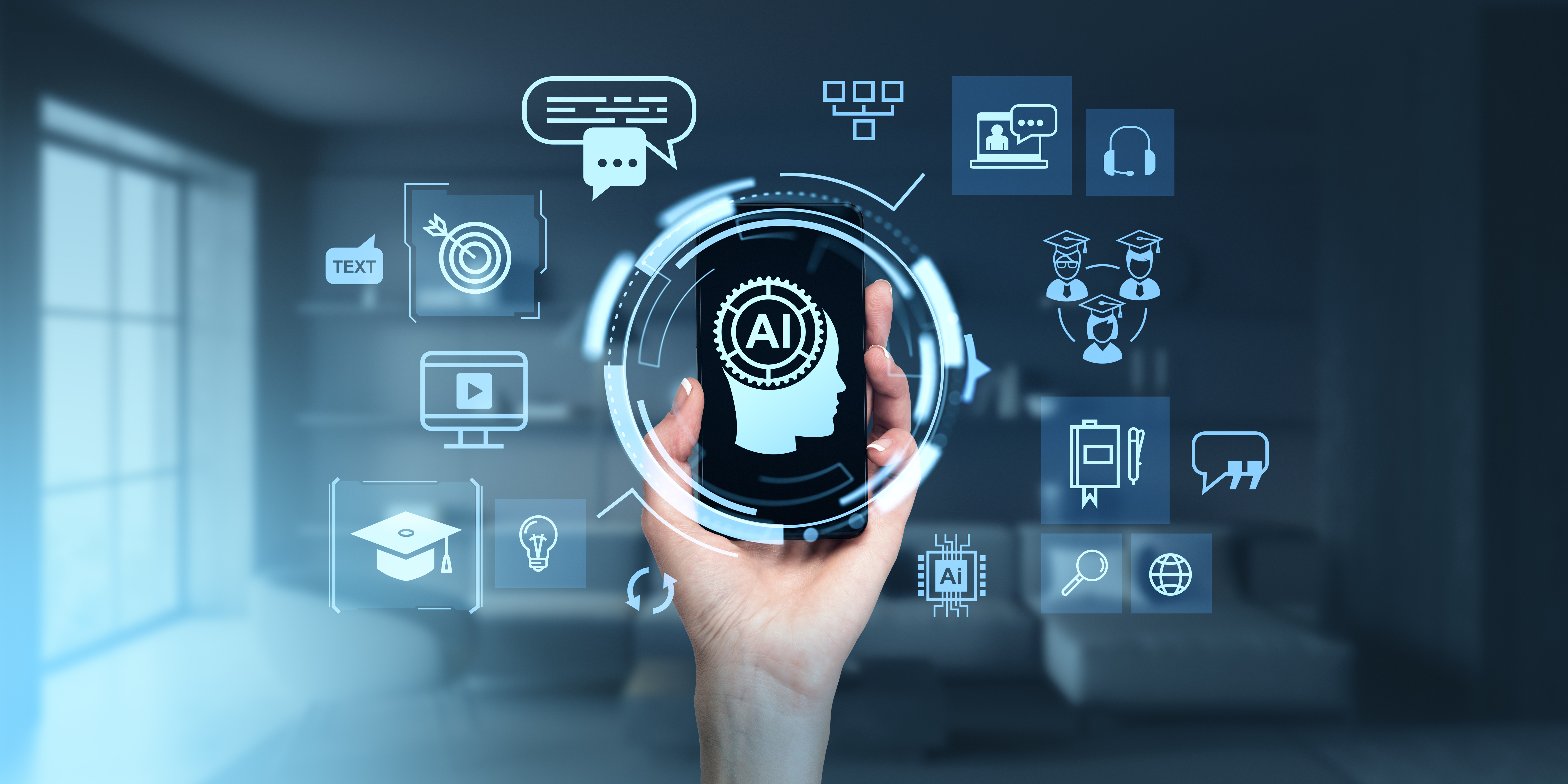
글로벌 시장 조사 업체인 ‘마켓 앤 마켓’은 제조 분야 AI 시장 규모가 2023년 32억 달러에서 2028년 208억 달러로 연 성장률 45.6%에 이를 것으로 전망했습니다. 실제로 여러 제조 기업들이 AI를 도입해 생산 비용을 줄이고, 제품 품질을 향상 나가고 있습니다. 이제 AI는 단순히 신기술이 아닌 제조 기업들의 경쟁력을 높이는 필수 역량으로 자리 잡아가고 있습니다.
그렇다면 디스플레이 산업에서는 AI를 어떻게 활용하고 있을까요? 삼성디스플레이는 제조 공정 및 연구 개발 분야에서 AI 기술을 도입하고 있는데요. 지금부터 삼성디스플레이의 혁신적인 AI 기술을 알아보겠습니다.
명화 스타일 합성에 적용되던 생성형 AI 기술이 디스플레이에도 사용된다!?
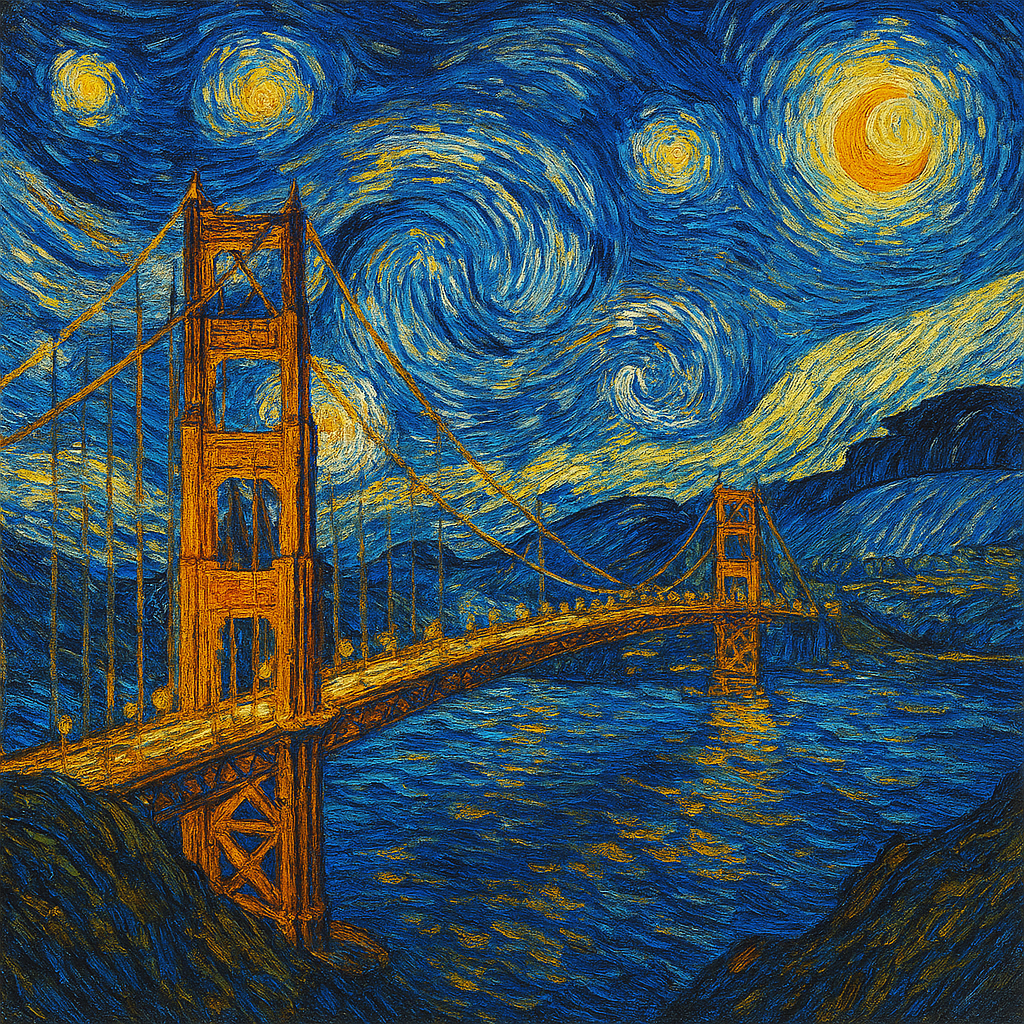
익숙한 ‘그’ 작품 같으면서도 어딘가 낯선 느낌의 이 그림, 바로 교량 이미지와 고흐의 ‘별이 빛나는 밤에’ 작품을 합성한 가상 이미지인데요. 이 작업에는 생성형 AI 기술인 ‘Neural Style Transfer(신경망 전환)’ 알고리즘이 사용됐습니다.
삼성디스플레이는 ‘23년 세계 최초로 디스플레이 분야에 ‘Neural Style Transfer(신경망 전환)’ 알고리즘을 적용한 ‘가상 이미지 활용 계측 기술’을 개발했습니다. 복잡한 과정을 거치지 않고도 계측에 필요한 패널 사진을 가상 이미지로 만들어 낼 수 있게 된 것이죠.
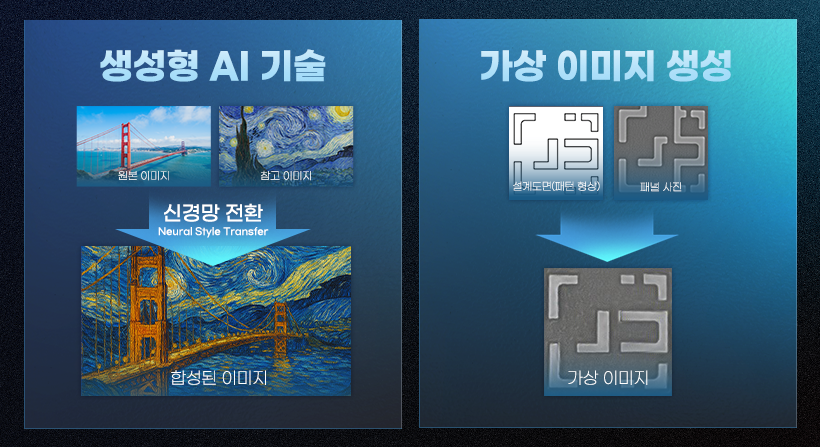
OLED 패널을 개발할 때 회로 패턴이 정확하게 설계대로 생성됐는지 확인하기 위해서는 기준이 되는 표준 샘플이 필요합니다. 기존에는 별도의 생산공정을 진행해 표준 샘플을 만들고 이를 촬영해 배선폭을 정확하게 계측한 후, 이후 생산되는 패널과 동일한 위치에서 배선폭을 비교했는데요.
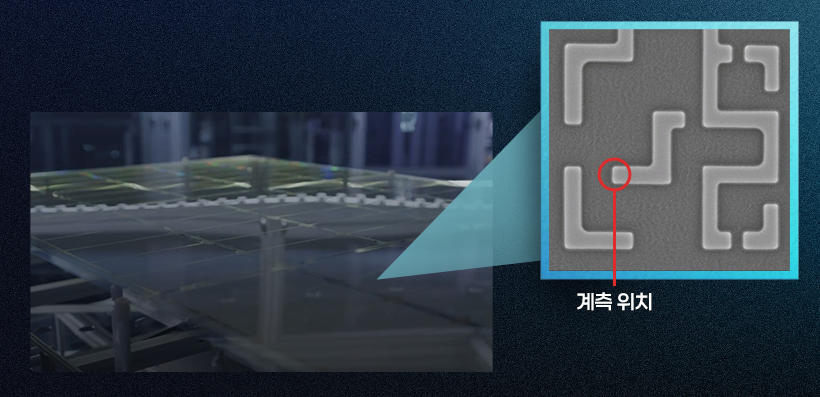
생성형 AI를 활용한 이후에, 별도의 공정 없이 생성형 AI가 만든 가상 이미지를 이용해 패널들의 배선폭을 손쉽게 비교할 수 있었습니다. 설계 도면으로부터 추출한 패턴 형상 이미지를 이전에 개발했던 패널 이미지와 합성해 가상 이미지를 생성할 수 있게 된 것이죠.
결과적으로 표준 샘플의 회로 패턴 사진을 얻기 위해 글라스를 별도로 투입할 필요가 없어졌고, 개발 과정도 대폭 단축돼 전체 제조공정 시간을 줄일 수 있게 됐습니다.
AI 기술로 설비 세팅도 간편하게, 계측 자동화 소프트웨어!
베트남 사업장에서 사용되고 있는 ‘계측 자동화 소프트웨어’는 AI를 활용해 설비 세팅 시간을 단축하는 기술인데요. 디스플레이 패널 생산 과정에서는 설비 세팅을 정확하고 정밀하게 ‘계측’해 공정 과정에서 생기는 고장 및 오류를 줄이는 것이 중요합니다.
기존에는 설비 점검 시 작업자가 직접 계측 장비와 태블릿을 가지고 측정한 탓에 여러 문제가 발생했습니다. 작업자 실수로 잘못 측정하거나 담당자에 따라 계측 편차가 발생하기도 했습니다. 또한 계측을 위해 설비 시설로 접근하는 과정에서 사고 위험도 있었습니다. 무엇보다 정확한 측정을 위해 공을 들이다 보니 작업에 많은 시간이 소요됐죠.
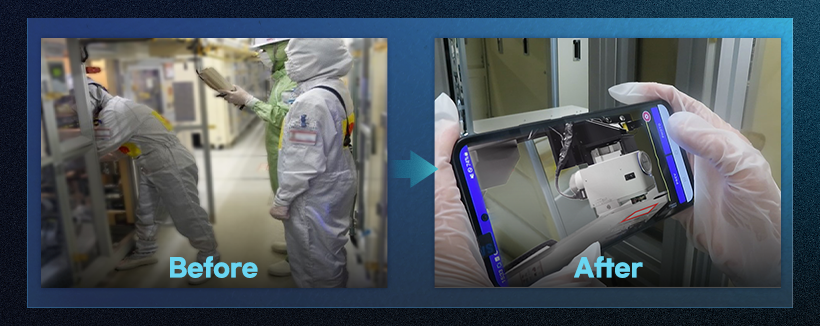
이를 해결하기 위해 삼성디스플레이는 AI 기술을 도입한 ‘계측 자동화 소프트웨어’를 개발했습니다. 기존에 번거로웠던 측정 과정을 한 번에 해결할 수 있는 시스템을 도입한 것인데요. 모바일 기기를 이용해 설비 기계를 촬영하면 AI가 설비 내 측정 영역을 추출한 뒤 자동으로 계측해, 작업자들이 손쉽게 측정 결괏값을 얻을 수 있도록 설계했습니다.
예를 들어, 패널을 들어주는 피커(Picker)와 패널 사이의 거리를 측정하는 경우를 생각해 봅시다. 작업자가 모바일 기기로 설비 영역 전체를 촬영하면, AI가 다양한 설비 내에서 피커와 패널을 자동으로 인식하여 이미지 모델로 추출합니다. 이후 설비와 패널의 모양과 크기를 추출한 뒤 AI가 거리를 자동으로 계측해 작업자에게 결괏값을 전달해 주는 것이죠.
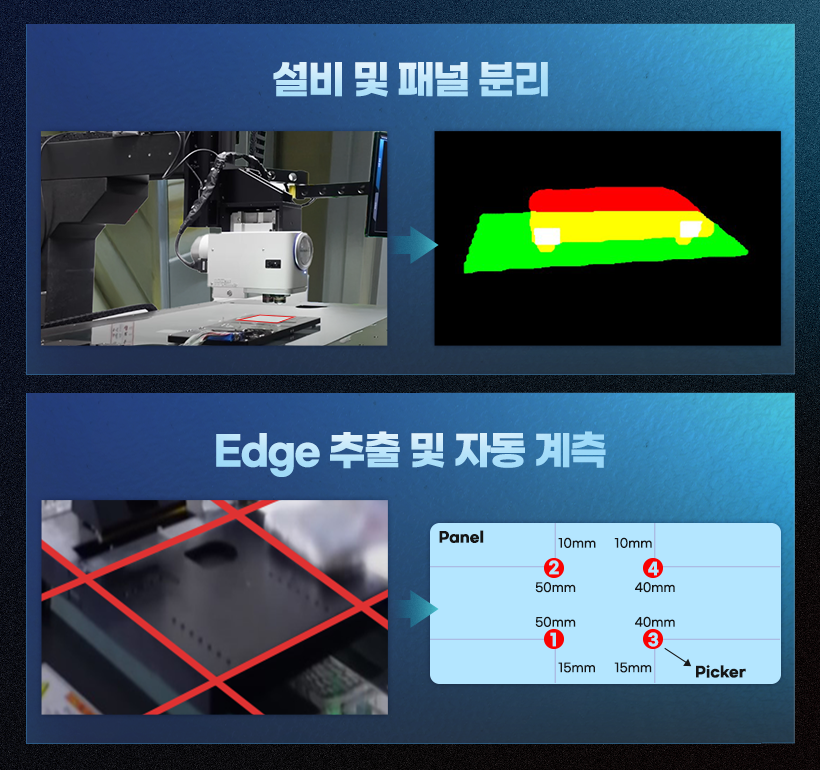
이렇게 AI를 활용해 복잡한 환경에서도 필요한 부품들에 대해서만 이미지를 추출할 수 있어, 보다 효율적인 업무 환경을 구축할 수 있었습니다. 그 결과, 작업자들의 설비 점검 시간이 2분 30초에서 10초로 대폭 단축됐고 AI 기반의 체계적인 시스템 덕에 점검 오차도 획기적으로 줄일 수 있었습니다.
신규 재료 설계도 AI가 스스로 뚝딱~!
이제 AI 기술은 디스플레이 재료 설계 과정에서도 핵심적인 역할을 수행하고 있습니다. OLED 디스플레이 성능에는 유기 소재의 효율과 수명이 많은 영향을 미칩니다. 그래서 원하는 성능을 얻기 위해 최적의 유기재료 구조를 찾는, 재료 설계 과정은 매우 중요하면서도 많은 시간을 필요로 하는데요.
삼성디스플레이는 생성형 AI로 천문학적인 경우의 수를 시뮬레이션해 최적의 재료 구조를 찾는 시스템을 개발했습니다. ‘분자 생성 AI’, ‘물성 예측 AI’, ‘합성 예측 AI’의 세 가지 AI 모델로 구성된 이 시스템은, 엔지니어가 기초 분자와 특성 값을 입력하면 AI가 스스로 시뮬레이션과 실험 데이터를 학습해 최적의 신규 분자구조를 생성해 주는 방식입니다.
기존에는 신규 재료를 설계하기 위해 엔지니어가 직접 분자구조를 바꿔가며 원하는 값에 가까운 것을 찾아야만 했습니다. 경우의 수를 따져 수없이 많은 분자 구조를 하나하나 설계하고, 또 직접 실험을 통해 결과를 확인하는 과정을 거쳐야 했죠. 워낙 방대한 작업이다 보니 한 달에 진행할 수 있는 작업 역시 한정적이었는데요.
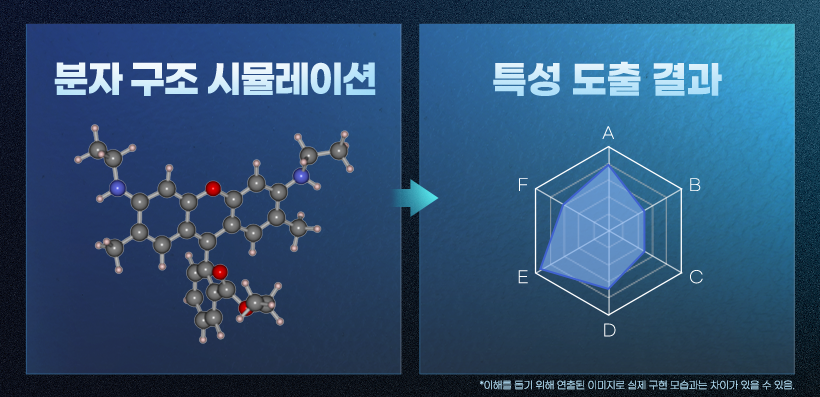
생성형 AI를 활용한 재료 설계 시스템을 도입한 이후에는 월 수백만 종이 넘는 새로운 유기재료 구조를 설계할 수 있게 돼, 결과적으로 업무 효율을 크게 향상시켰습니다.
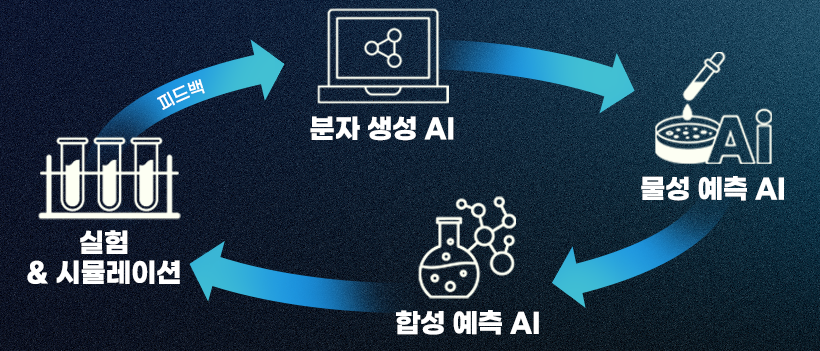
이제 AI 기술은 기존의 한계를 극복하고 디스플레이 산업에 혁신을 가져오는 새로운 성장 동력이 되고 있는데요. 디스플레이 제조공정은 물론 연구개발 과정에서 점점 더 핵심적인 역할을 하고 있습니다. 앞으로 AI 기술이 더 발전한다면 디스플레이 분야에서도 더욱 혁신적인 방식과 기술들이 탄생하지 않을까요? AI로 더욱 빠르게 발전하고 성장해 나갈 삼성디스플레이를 기대해 주세요.